Turbocharger with potential for rapid demand expansion
Turbochargers, in their heyday in the 1980s, were installed in many racing cars and sports cars to enhance the speed and maximum output of the automobiles. In those days, there was a trade-off relationship between the turbocharger and fuel consumption. Recently, a turbocharger has attracted attention once again as a device for boosting the insufficient output of engines that are downsized to meet environmental restrictions. Thus, its arena of applications has been expanded to general automobiles and eco-cars as well.
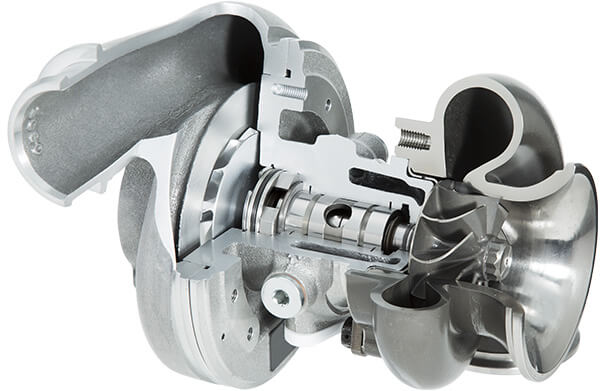
Organic combination of rotary components and technologies cultivated in machine processing
Technologies cultivated in the production of rotary components and machined components are incorporated cross-sectionally in the electromagnetic technology, winding technology and stamping technology of the resolver. We produce high-precision resolvers by combining multiple technologies that only a comprehensive precision equipment manufacturer can realize.
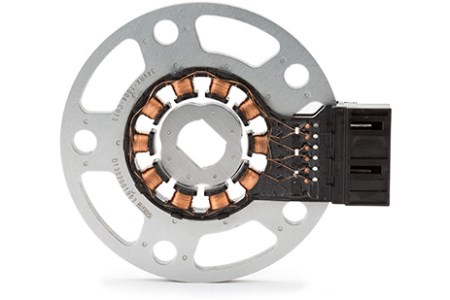
The speed of the motor that is the heart of the electric vehicle, Nissan LEAF, is controlled.
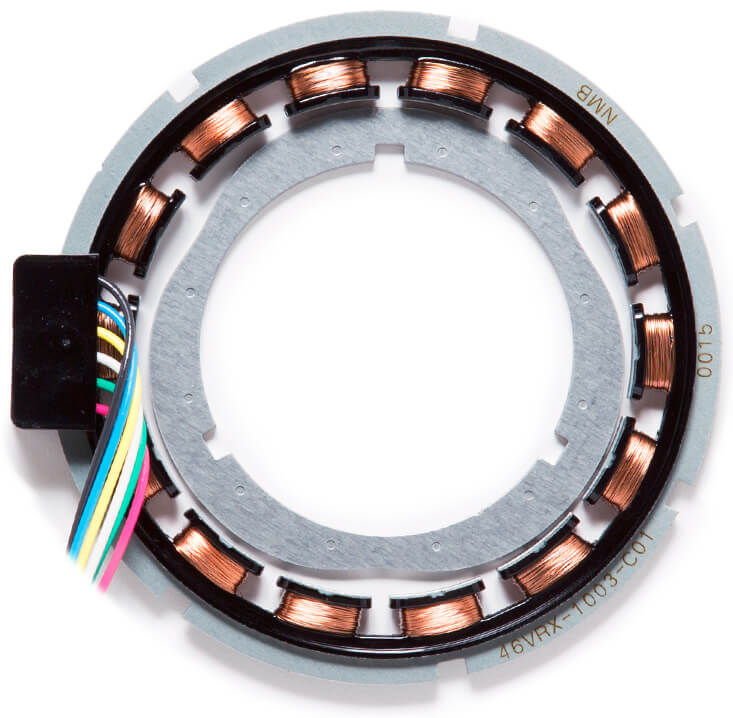
Winding technology that influences position detection accuracy
One of the parts that greatly influence the accuracy of a resolver is winding provided in the stator. The angle is detected by means of an electric signal generated due to the change in reactance of the rotating rotor and fixed stator. Stable characteristic is maintained by making the winding even. New VR resolvers of Minebea is precisely adjusted at the design stage to achieve higher accuracy. In addition, to improve resolver performance and realize its mass production, the copper wire it contains must be wound fast and evenly.
Minebea’s know-how in motor production was utilized here. We applied our expertise in winding technology obtained through motor production to the resolver, and this made it possible to have faster copper wire winding than ever before. Furthermore, we designed in-house unique nozzles that are based on the diameter of the copper wire, and they are used for passing the copper wire. This allowed copper wire winding to be tight, highly accurate and stable.
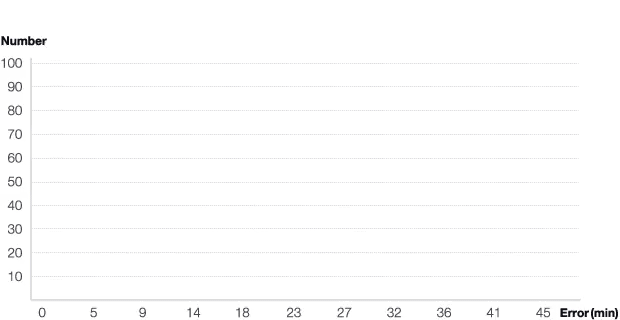
Welding technology for high durability
The resolver that directly affects the motor requires not only high accuracy but also superior durability. In developing the VR resolver, Minebea focused on the connection between the copper wire and terminal. To enhance durability, we adopted TIG (Tungsten Inert Gas) welding instead of regular soldering. And to securely connect them, we melt the upper part of the wire-wound terminal to make a ball shape and enfold the wire with the melted ball. This method is also
advantageous since welding quality can be easily controlled by visually checking the ball shape. Defects can be easily found if the ball is bent or collapsed. To realize this, peeling of the copper wire coating and welding must be done simultaneously, and this requires advanced technology. We have realized highly difficult TIG welding and kept superior durability and quality by applying our equipment condition setting technology that is one of the pillars supporting Minebea.
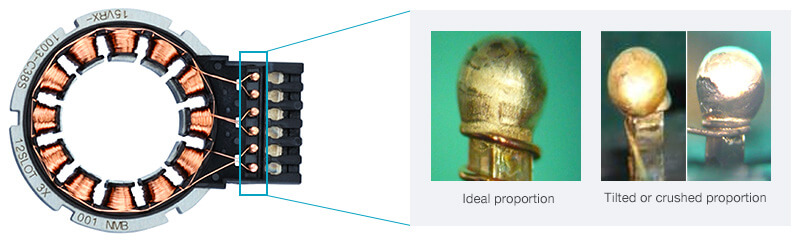